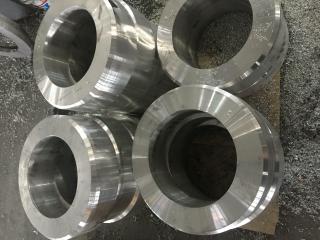
Description
Scope of supply of Aviation Group:
Round rods, steel plates, non-standard forgings, rings, etc., welcome to inquire!
1. Introduction to SKD11 Materials
SKD11 is a universal cold work mold steel with high wear resistance, high-carbon and high-chromium alloy tool steel and vacuum degassing refined steel. The steel is pure, with good hardening and low quenching deformation. The steel is softened by spherical annealing and softening, and has good processability and the carbide particles are small and uniform. There is no need to worry about the special addition of molybdenum and vanadium for quenching and cracking.
Chinese GB standard grade Cr12Mo 1 V, German DlN standard material number 1.2601, Japanese Jis standard grade SKD11, American AISi/sAE standard grade D2
2. Chemical composition of SKD11
alloy | % | Chromium Cr | Stone Mo | Copper with | Vanadium V | Ni | Carbon C | Manganese Mn | Silicon Si | Phosphorus P | Sulfur S |
Cr12Mo1V
SKD11 |
Minimum value | 11.0 | 0.80 | – | 0.20 | – | 1.40 | – | – | – | – |
Maximum value | 13.0 | 1.20 | 0.25 | 0.50 | 0.50 | 1.60 | 0.60 | 0.40 | 0.030 | 0.030 |
3. SKD11 features
1. Good high-temperature strength and toughness, good wear resistance and easy to cut;
2. SKD11 is a cold mold steel with high strength, toughness and heat resistance. In recent years, with the development of isotropic products, it has been developing towards high toughness and other aspects. It can make the mold life longer, its performance is more stable, and it is easy to process, and it has less deformation in heat treatment.
SKD11 mold steel product features:
(1) Vacuum degassing is carried out, so the internal quality is extremely clean.
(2) Good machining.
(3) Good hardenability, it can harden by air cooling, and there is no need to worry about quenching and cracking.
(4) The heat treatment deformation is very small and the quenching deviation is extremely small. It is most suitable for molds with precision requirements.
(5) Extremely excellent wear resistance, and is most suitable for use as a punching die for stainless steel or high-hard materials.
(6) Good toughness.
SKD11 deep cooling treatment
To obtain the highest hardness and dimensional stability, the mold is immediately deep-cold to -70 degrees Celsius to -80 degrees Celsius after quenching, and maintained for 3-4 hours, and then tempered. The hardness of the tool or mold after deep-cold treatment is 1-3 HRC higher than that of conventional heat treatment. For parts with complex shapes and large size changes, deep-cold treatment can cause cracking.
SKD11 Nitriding Treatment
After the mold or workpiece is nitrided, a layer of hardened tissue with high hardness and certain corrosion resistance is formed on the surface.
During nitriding at 525°C, the surface hardness of the workpiece is about 1250 HV, and the impact of nitriding time on the permeation layer is shown in the table below. Nitriding time (hours) 20 30 60 Nitriding layer depth mm 0.25 0.30 0.35
The hardness of the workpiece surface layer was about 950 HV at soft nitriding treatment at 570°C. Usually, the soft nitriding treatment is 2 hours, and the hardened layer depth can reach 10-20um. The mold blank is grinding or working in a low-temperature tempering state, and grinding is prone to grinding cracking. To prevent cracks from occurring, a small grinding feed should be used to grind multiple times, and good water cooling conditions should be added.
When wire cutting is used for molds with complex shapes or large sizes, cracking usually occurs when the final line is used for wire cutting.
To prevent cracking, it is recommended to use gas quenching and high-temperature tempering to reduce heat treatment stress or to perform cavity preprocessing of mold embryos.
SKD11 heat treatment
Quenching: Preheat first 700-750℃, then heat to 1000-1050℃ and cool in stationary air. If the thickness of the steel is above 6 inches, heat to 980-1030℃ and harden in oil.
Backtemper: Heat to 150-200°C, stay at this temperature, and then cool in stationary air.
Hardness: HRC 61 or above.
Annealing: Heat to 800-850°C, stay at this temperature for 1-3 hours, and let it gradually cool in the furnace.
Forging: 1050~950℃.
SKD11 quenching and tempering specifications
The quenching temperature is 1010°C, air-cooled, the tempering temperature is 200°C, and the hardness is 58~60HRC.
4. DC53 application field
- Used to make plastic molds, scissors, circular saw blades, hardware stamping molds, forming and rolling rollers
- Make cold or hot work dressing molds, roller edges, silk patterns, wire molds, transformer core punching molds, cutting steel leather rolling knife, steel pipe forming rollers, special forming cylinders, nail head molds, etc.
- High-efficiency blanking die, punching die, and stamping die with thin steel plate with thickness ≤6mm
- Various scissors, inlay parts, and wire rubbing molds.
- Sliding resistant cold heading mold, deep drawing forming mold, cold extrusion mold.
- Thermoset resin type, general plastic mold.