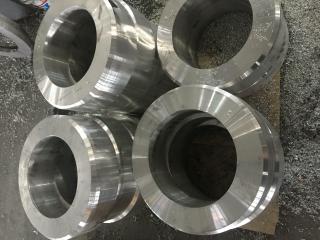
Nimonic80A High Temperature Alloy
Description
1. Introduction to Nimonic80A materials
Nimonic 80A is a British grade, corresponding to the Chinese grade GH80A. It is a nickel-based alloy with excellent high temperature and corrosion resistance. It mainly consists of Ni and Cr as the main components. Aluminum and titanium are added to form a high-temperature alloy with diffusion reinforcement in γ′ phase. Except for the slightly higher aluminum content, the other ones are similar to GH4033, and the service temperature is 700-800℃, and have good creep resistance and oxidation resistance at 650-850℃. The alloy has good cold and hot processing performance and mainly supplies hot rolled bars, cold-pulled bars, hot-rolled sheets, cold-rolled sheets, strips and rings.
2. Nimonic80A execution standard
WS9-7009-1996 “Hot Rolled Rods for GH80A Alloy Turbine Blades”
WS9-7011-1996 “GH80A alloy hot rolling, forged and cold-pulled rod”
WS9-7012 Ring Parts-1996 “GH80A Alloy Rolled Ring Parts”
WS9-7095-1996 “GH80A alloy hot-rolled sheets, cold-rolled sheets and strips”
3. Chemical composition of Nimonic80A
Implement in accordance with the national standards, US standards and British standards
4. Nimonic80A physical properties
Nimonic80A density ρ=8.15g/cm3
Nimonic80A melting point 1405℃
Nimonic80A electrical properties room temperature ρ=1.23×10-6Ω.m
Nimonic80A magnetic properties are non-magnetic.
Nimonic80A antioxidant properties The oxidation rate of Nimonic80A was tested in air media for 100h:
700 θ/℃-0.037g/(m2·h); 750 θ/℃-0.041g/(m2·h); 800 θ/℃-0.047g/(m2·h);
4.1 GH80A phase change temperature
4.2 GH80A time-temperature-tissue transition curve
4.3 The structure of the GH80A alloy blade blank is treated according to different heat treatment specifications: 1080℃±10℃, 8h, air-cooling treatment: at 1080℃, some M7C3 and M23C6 grain boundary carbides in the matrix dissolve into the solid solution. During the cooling process, M7C3 and M23C6 chromium-rich carbides are formed in the grain boundary. M7C3 precipitates out at about 1000°C and converts to M23C6 at a lower temperature. M23C6 precipitates at 750-1000°C and can also nucleate independently to generate grain boundary carbides. Therefore, after 1080℃±10℃, 8h, air-cooling treatment, M7C3 and M23C6 in discontinuous states appear on the grain boundary, with γ′ phase and MC in the crystal.
1080℃±10℃, 8h, air-cooling + 700℃±5℃, 16h, air-cooling treatment: The alloy is aged by 700℃±5℃, 16h on the solid solution structure, and the M7C3 on the grain boundary continues to be transformed into M23C6, so a continuous M23C6 is precipitated on the grain boundary, and the γ′ phase in the crystal also grows into spherical particles [4]
Nimonic80A heat treatment system:
blade rods are: 1080℃±10℃, 8h, air-cooled + 700℃±5℃, 16h, air-cooled.
Hot rolling, forged and cold-pulled bars: according to the provisions of Table 1-2.
Rolled ring parts: (1050~1080℃)±10℃, not more than 2h, water-cooled +750℃±5℃ (or +700℃±5℃), 4h (or 16h), air-cooled.
Hot rolled sheets, cold rolled sheets and strips are: supply state +750℃±10℃, 4h, air-cooled.
Nimonic80A smelting and casting process Rods and plates for blades are adopted for vacuum induction smelting plus electroslag remelting process. The rolled ring parts and hot-rolled, forged and cold-pulled rods are processed by induction smelting and electroslag remelting, or vacuum induction smelting and vacuum arc remelting, or vacuum induction smelting and electroslag remelting.
V. Nimonic80A process performance and requirements
5.1 Nimonic80A forming performance
5.1.1 Nimonic80A forging alloy has good forging properties. The heating temperature of the steel ingot is 1120~1150℃, and the forging temperature is not less than 1000℃. The forging temperature shall not be lower than 950℃[2].
5.1.2 The heating temperature of Nimonic80A hot-rolled plate is 1120~1150℃, and the rolling stop temperature is not lower than 930℃ [2].
5.1.3 The blanks for forging turbine blades of Nimonic80A turbine blades should be sprayed with protective lubricant according to the prescribed process requirements, and can only be heated in the furnace after drying. The parts blanks are heated in an electric furnace, the furnace loading temperature is 800℃±20℃, the insulation is 60 minutes, the heating temperature is 1090℃±10℃, the insulation is 35 minutes, the opening forging temperature is 1090℃, and the stop forging temperature is 950℃. Forging is carried out on the forging machine, and the mold chamber is lubricated with molybdenum disulfide before forging. The intermediate process of forging parts blanks should undergo solid solution treatment, with a heating temperature of 1130℃±10℃, insulation for 60 minutes, and air-cooled. After blowing sand, spray protective lubricant according to the prescribed process requirements, dry it and heat it into the furnace. The parts blanks are then loaded, heated and insulated according to the above regulations, and final forging is performed on the crank press, and the mold chamber is lubricated with molybdenum disulfide before forging.
5.2 Nimonic 80A welding performance alloy can be automatically connected to argon arc welding and seam welding.
Note: Before welding, grind the sample with a sand cloth and clean it with acetone. The board is not more than 1.2mm thick and does not have welding wires. Weld it in one piece.
6. Nimonic80A application field
Used to manufacture engine rotor blades, guide blade support, bolts, vane lock plates and other parts.
Nimonic 80A can also be used in high-temperature components in nuclear reactors, such as nuclear fuel elements, reactor materials, etc.