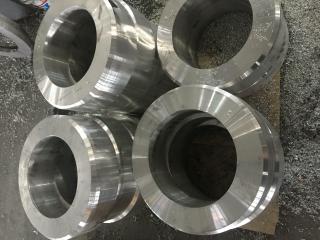
Description
1. Introduction to GH5605/605 Materials
GH5605 is a CO-Cr-Ni-based solid solution reinforced deformation high-temperature alloy with a service temperature below 1000 degrees Celsius. NI-Cr and W were added to the alloy for solid solution strengthening. The alloy has high strength and resistance to yang. It also has good elastic modulus, wear resistance and welding performance. The addition of trace amounts of rare earth element yttrium improves the performance of hot processing plasticity and cold forming process. The main products include hot rods 10~100mm, forged rods: 100mm~350mm, cold-tied thin plate 0.05mm-4.0mm, hot rods: 4mm~14mm, with 2mm-10mm, and various non-standard forgings.
2. Chemical composition of GH5605/605
alloy | % | C | Cr | In | Co | W | Fe | S | P | And | Mn |
GH5605/605 | Minimum value | 0.05 | 19.0 | 9.0 | margin | 14.0 | – | – | – | – | 1.0 |
Maximum value | 0.15 | 21.0 | 11.0 | 16.0 | 3.0 | 0.030 | 0.040 | 0.40 | 2.0 |
3. GH5605/605 Standard:
WS9 7053-1996 “GH605 Alloy Hot Rolled Sheets, Cold Rolled Thin Sheets and Strips”
Q/5B 4021-1992 “GH605 Alloy Ring Forging Technical Conditions”
Q/5B 4031-1992 “GH605 Alloy Rods”
Q/5B 4032-1992 “GH605 Alloy Strips”
Q/5B 4033-1992 “GH605 Alloy Strips (Hard)”
Q/5B 4059-1992 “GH605 High Temperature Alloy Cold-pull Welding Wire”
4. GH5605/605 Physical properties:
density | Melting point | Thermal conductivity | Specific heat capacity | Elastic modulus | Shear modulus | Resistivity | Poisson’s | Coefficient of linear expansion |
g / cm3 | ℃ | λ/(W/m?℃) | J/kg?℃ | GPa | GPa | μΩ?m | a/10-6℃-1 | |
9.13 | 1330 | 0.5(100℃) | 377 | 231 | 89 | 1.12 | 0.286 | 12.9(20~100℃) |
GH605 mechanical properties: (small value of mechanical properties detected at 20℃)
Heat treatment method | Tensile strength σb/MPa | Yield strength σp0.2/MPa | Elongation σ5/% | Brinell hardness HBS |
Solid solution treatment | 960 | 340 | 35 | 282 |
V. GH5605/605 Application Areas
Suitable for manufacturing hot-end high-temperature components such as engine combustion chambers and guide blades that require medium strength and excellent high-temperature oxidation resistance.
It is often used to manufacture high-temperature components such as guide plates, turbine outer rings, outer walls, vortex plates, and sealing plates on engines and aircraft.
New brush seals for making engines.